Weeks commencing 9, 16 and 23 September
After the refitting of the tender wheels to the frames we then moved on to fitting the tank. The hire lifting gear had already been organised for collection and I met one of the Engineering Team at the hirer’s site to collect the first instalment. The volunteer offering to transport the gear for us so saving us the cost. However, the gear wasn’t ready for us, and the employee in the yard, though keen enough, couldn’t find the items we were to collect. After spending a lot of time walking around the yard we eventually got away with what we could find. Unfortunately, this took most of the day, when it should have taken a few hours. As can be expected our volunteer delivery driver wasn’t too happy with the thought of repeating the process the next day for the second consignment. So I contacted the hirer who were apologetic and immediately organised the delivery of the outstanding items the next morning with their own transport.
With the gear on site it was divided up in to the four corners of the tank. As the tank was to be lifted in four corners at once a big team was required so I won’t mention all the names present but thanks for turning out. With the tank up in the air the assembled frames were rolled under the tank. With the frames chocked the tank was then carefully lowered. As the tank neared the frames, the frames were moved and the tank jacked sideways for fine adjustment. As when the frames were lowered on to the wheels, the tank went in to place very easily. The sump and the brake cylinders slotting between the installed pipework. A tribute to the accurate fitting of the new pipe runs.
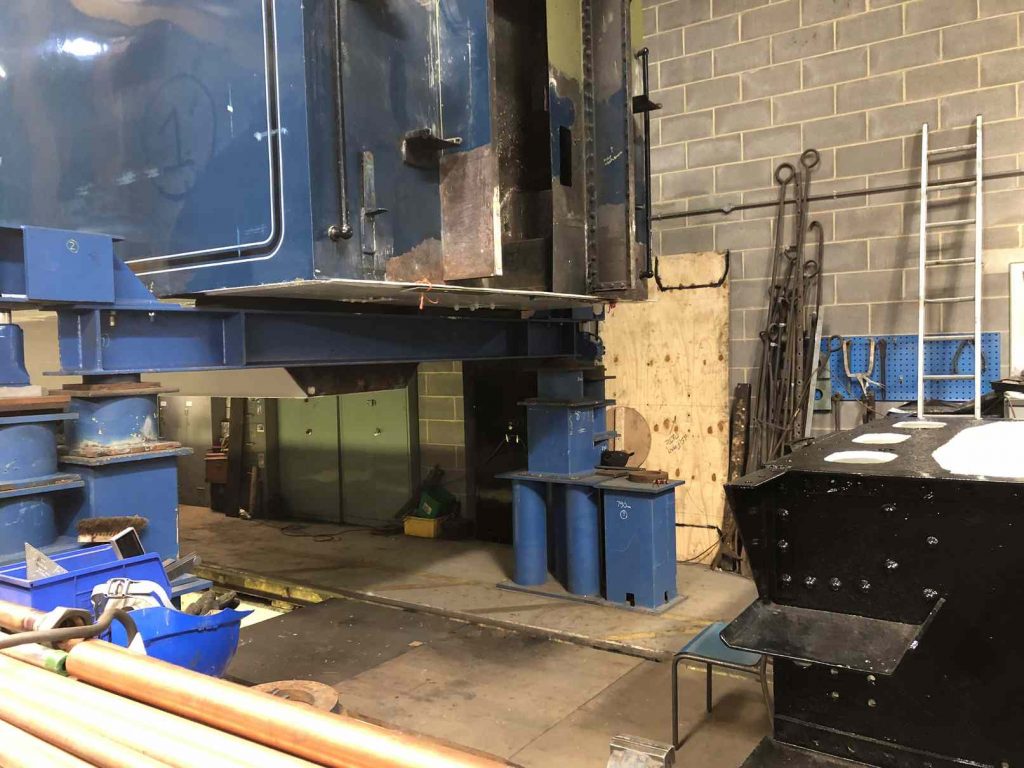
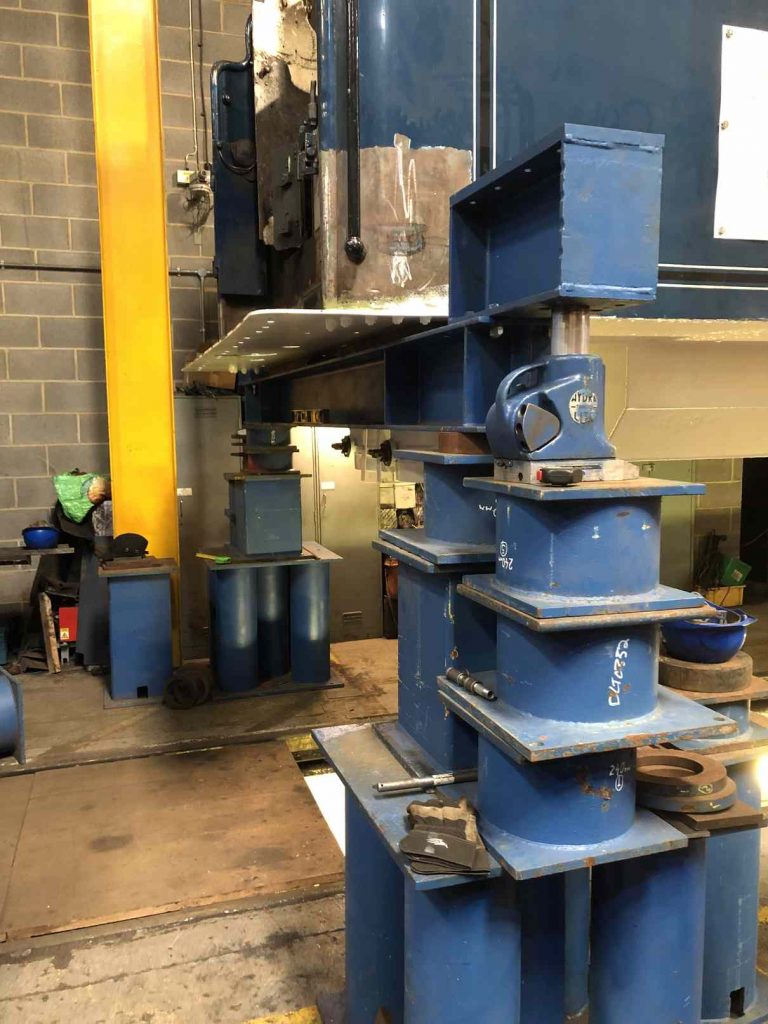
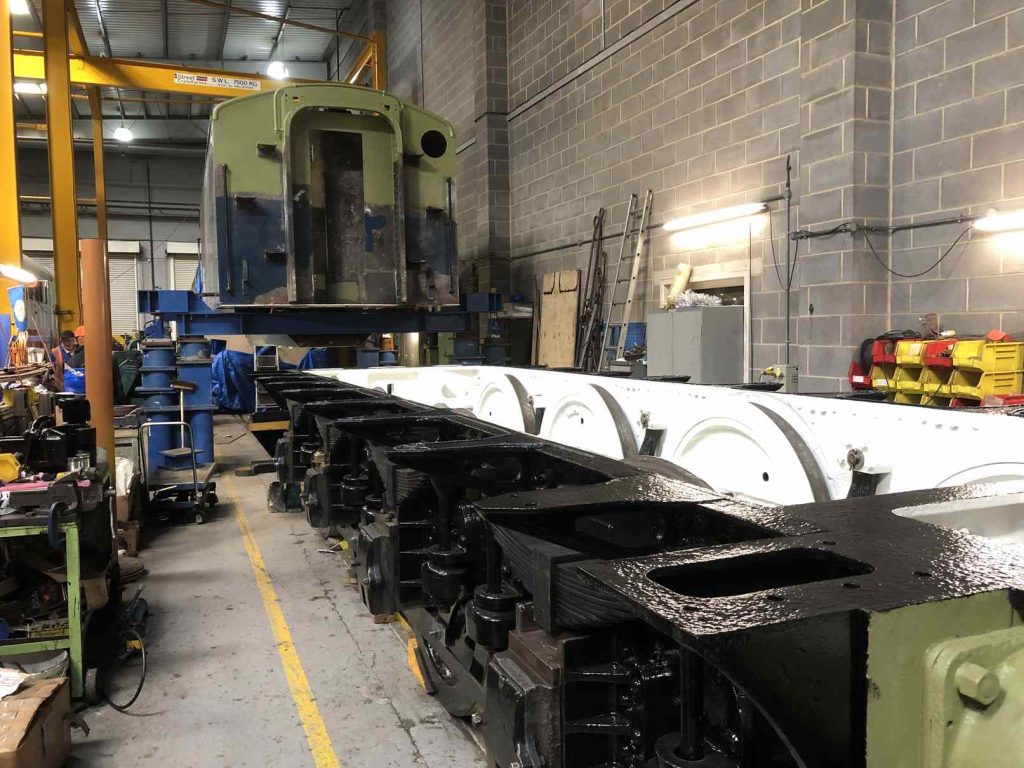
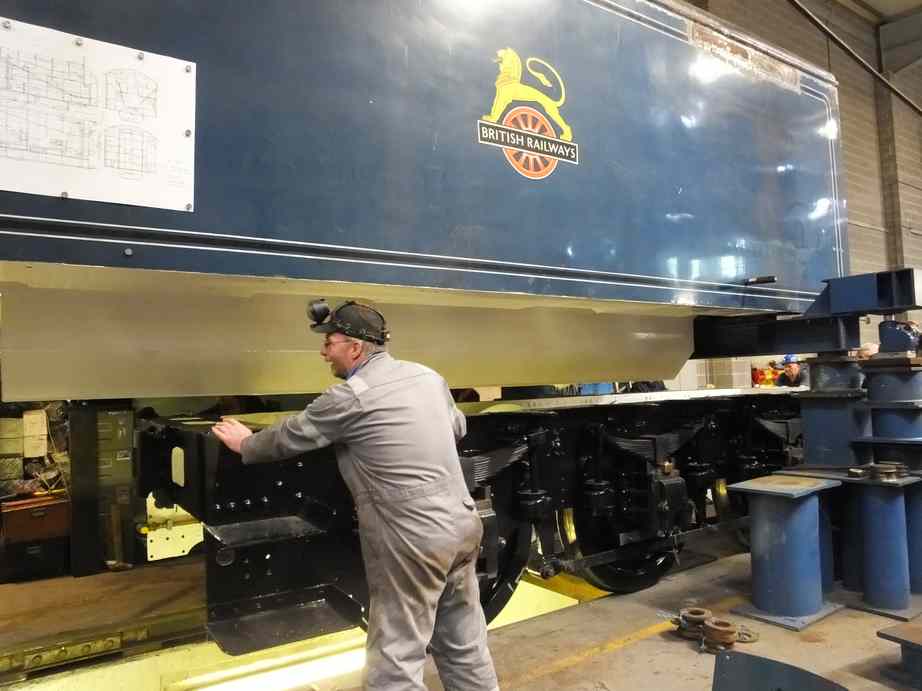
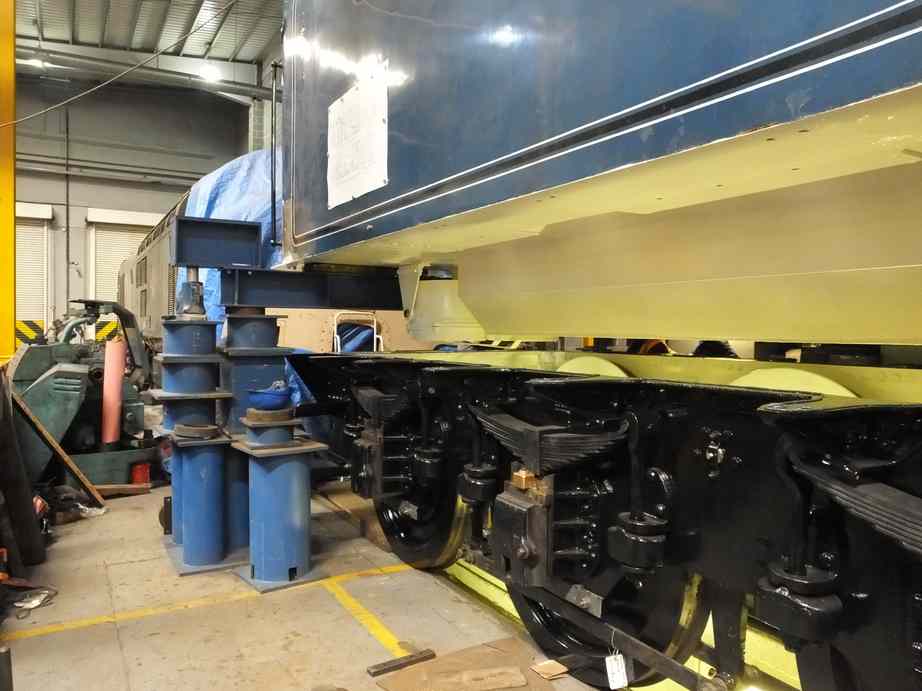
With the tank down on the frames the lifting gear was moved to the back door of the workshop and collected the next day. The return load including the large stools and beams the tank has stood on for the last year. Some of the lifting gear is very heavy and I thank the NRM workshop staff for their help with the forklift truck.
The tank lift was completed over two days. At the end of the first day the tank was stood on packing on the frames and the leading beam was moved forward. This allowed the areas where the tank had stood to be uncovered for painting. Thanks go to the painting team who stayed late and then had an early start the next day to put paint on these areas ready for the final fitting of the tank.
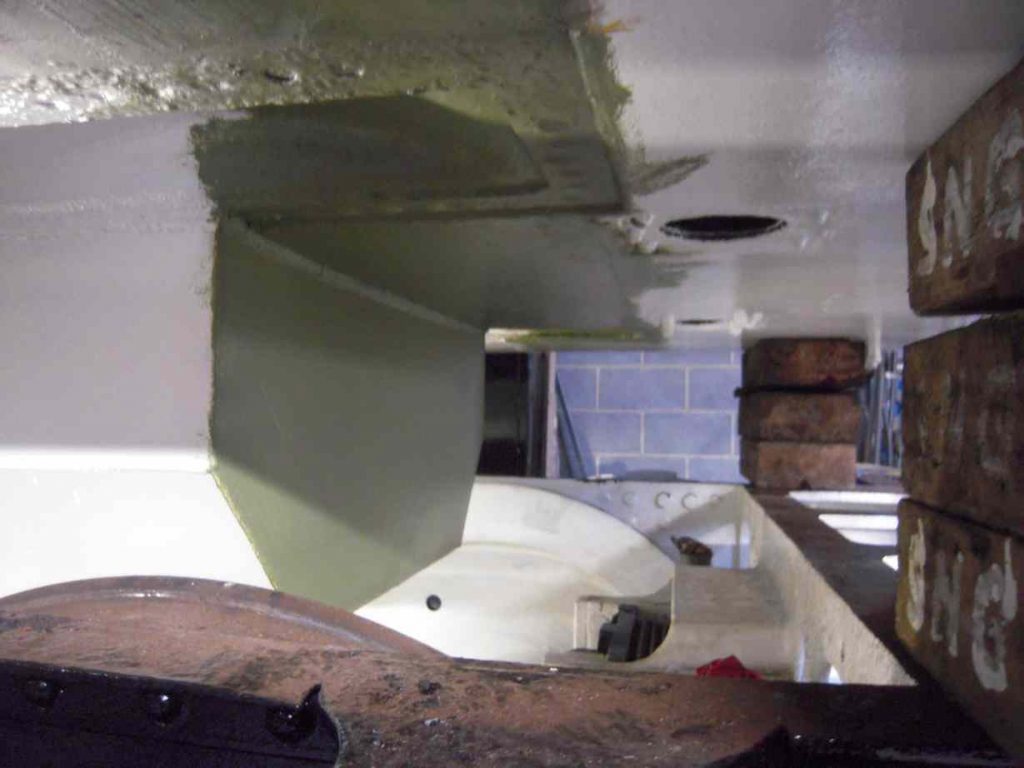
With the tank on the frames some of the bolts were put through to temporarily locate the tank, most of them easily dropping through the holes in the tank into the brackets on the frames. The bolts across the leading dragbox have now been permanently fitted. The holes for the bolts in the tank are being cleaned up before the bolts in there are permanently sealed in to provide water tightness.
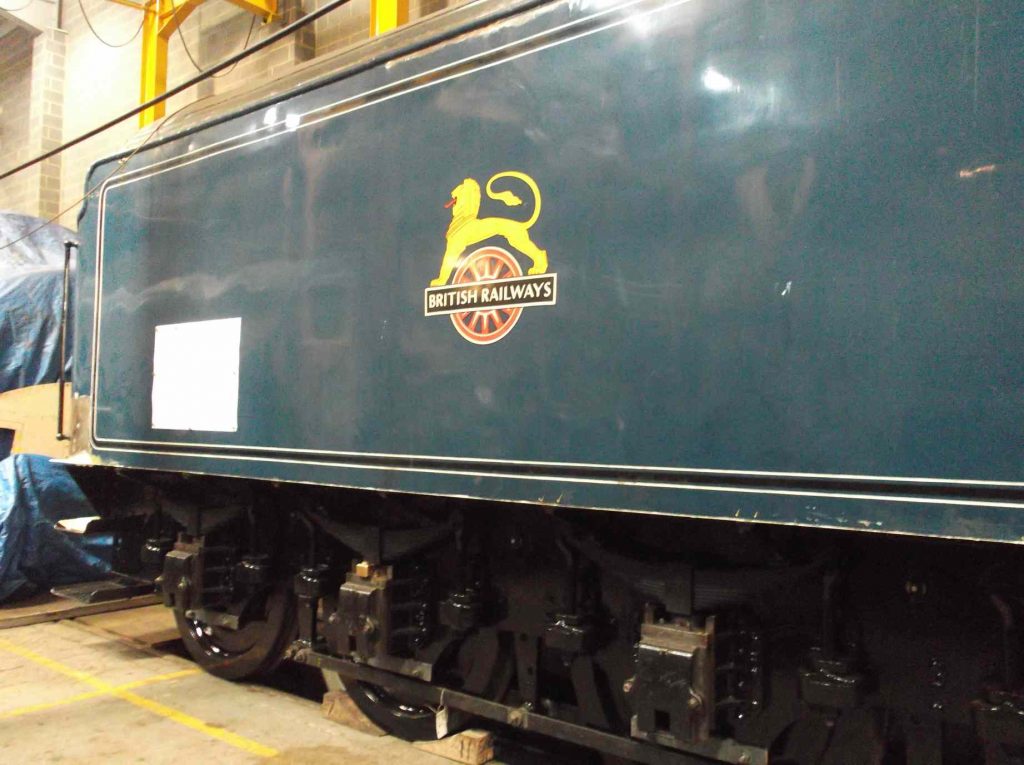
Before the tank was fitted the last of the pipe runs through tender frames were pressure-tested, and passed off as tight. Also the last of the washering on the top tender spring hanger pins, this being completed the day before the tender lift with the fitting of some custom made spacer washers.
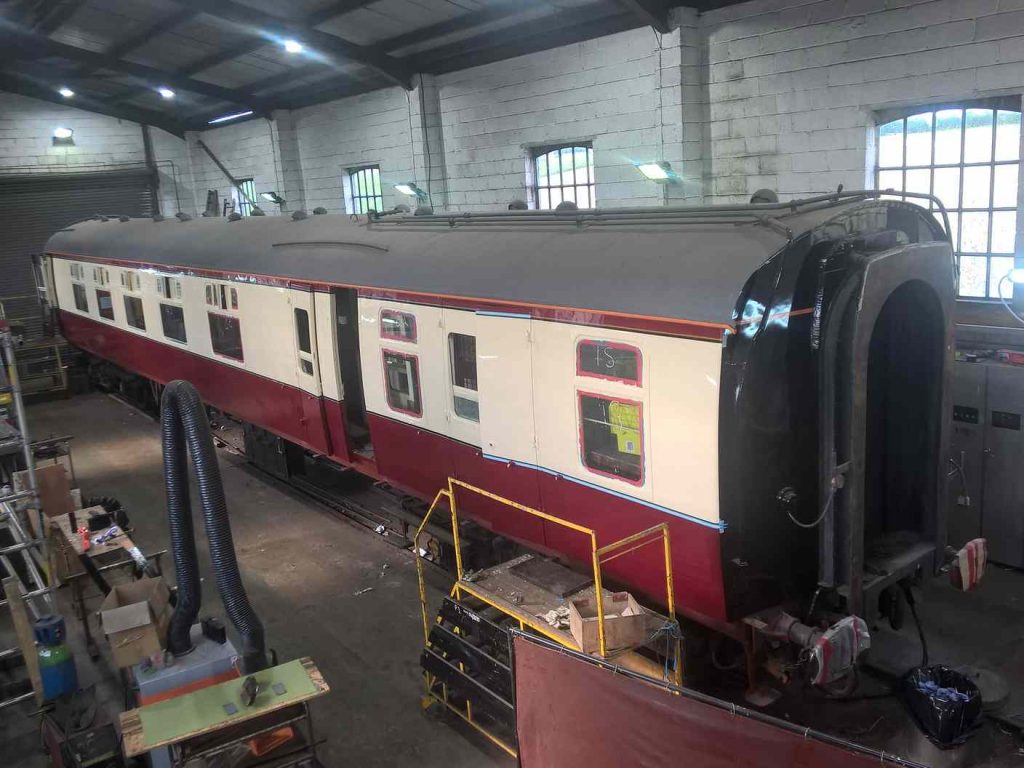
The tender brake shaft has now been fitted and the brake cylinder piston rods refitted. The leading intermediate brake hanger tie, bolts through the hangers. The tie is a bit of a rough fabrication, put on after the abandonment of the water pick up scoop. It does not fit very well so we have been working on the arrangement to remove wear and get a better fit. The trailing tie rod has been welded around one end to build up the material around the pin holes.
The long tender brake pulls were checked for fit on the newly installed refurbished brake gear, and they fit well. They have now been removed and stripped for NDT, having previously been rebushed.
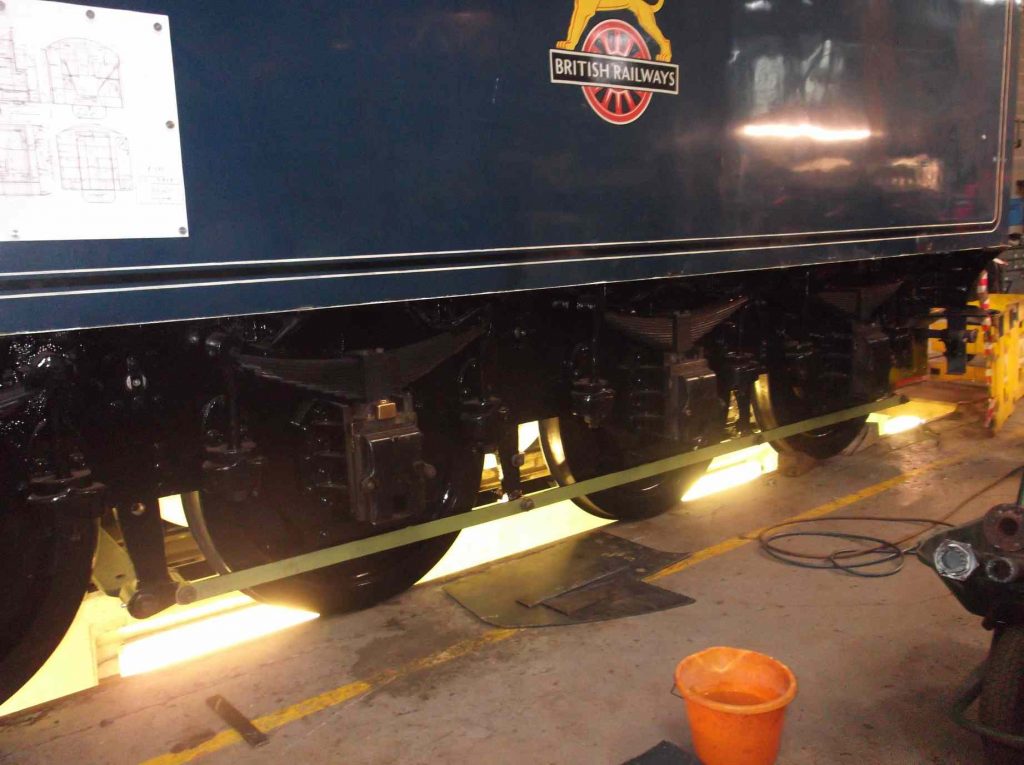
All the new tender hornstay bolts have been fitted and flogged up.
On the front of the tender tank work has concentrated on removing the plate and angles making up the handbrake shelf and lower locker fronts. New material has been obtained to replace the removed steel.
When we were loading the tender springs it was noticed there was a variation in the nut sizes on the spring hangers. There’s a mix of pre and postwar nuts, and another couple of odd sizes. It would be preferable to standardise on the nut size. As the prewar ones may have been with us for a very long time it would be nice to keep them, but they have to be specially made now, and we can’t make prewar nuts from the postwar ones as they are bigger. So it was decided to remove the odd nuts and machine them down to the postwar size. Now we have the right number of each type to ensure that when we change a spring we’ll only need one spanner. To accommodate the postwar nuts we couldn’t find the correct spanner in our collection, so one has been bought off ebay and it will be part of the loco’s toolkit.
The fitting of the new motion pins continues with the taper pins being fitted to the outside gear. The new pins for the inside, conjugated gear are now at York.
Work on the cod’s mouth gear continues. One of the ball bearings is heavily worn, with grit in the bearing, so we have obtained a new sealed bearing and this will be fitted. Another new bronze bush has also been made to replace a worn one. Wear to one of the shafts has been repaired by welding it up and machining it back to size. The arrangement has also been altered to ensure that the gear can be assembled without excessively stressing the ball bearing by incorrectly loading them.
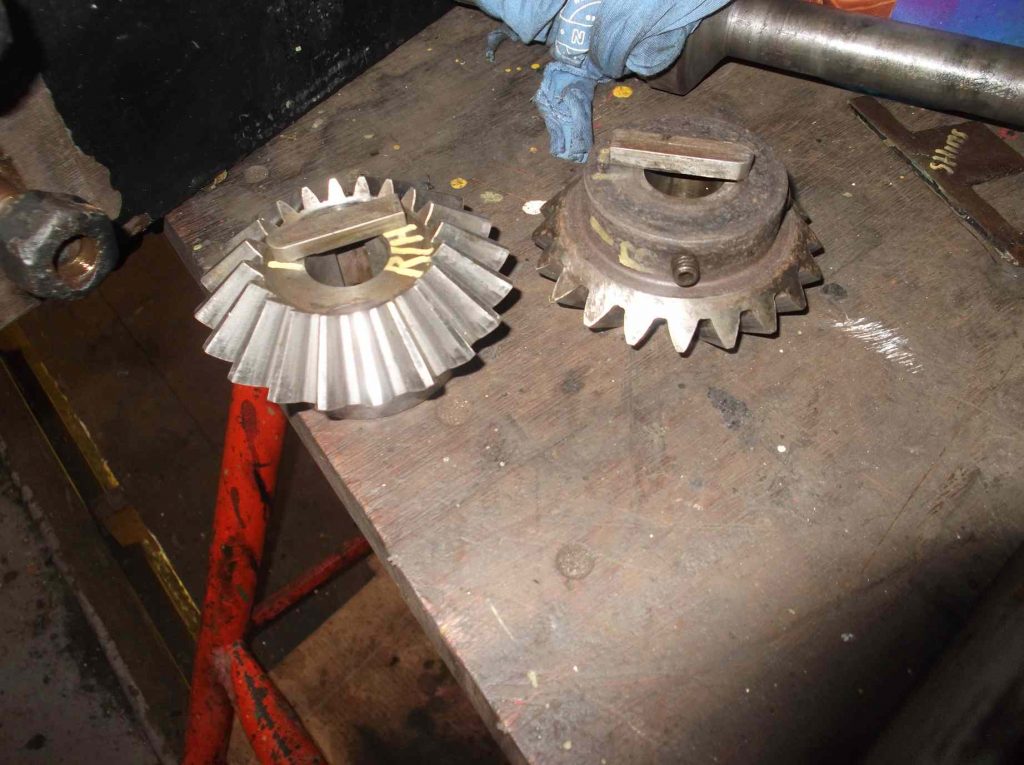
Work continues on the return cranks with machining of the faces giving the correct distances relative to the crank boss.
The middle slide bar bolts were completed by drilling through for the split pins. The slidebars and crosshead were put in and bolted up. After a final flogging the split pins were fitted. Before the crosshead was fitted it’s bearing surfaces were given a final inspection and the gudgeon pin was given a final lap in. The right crosshead is now receiving the same attention in preparation for it’s fitting.
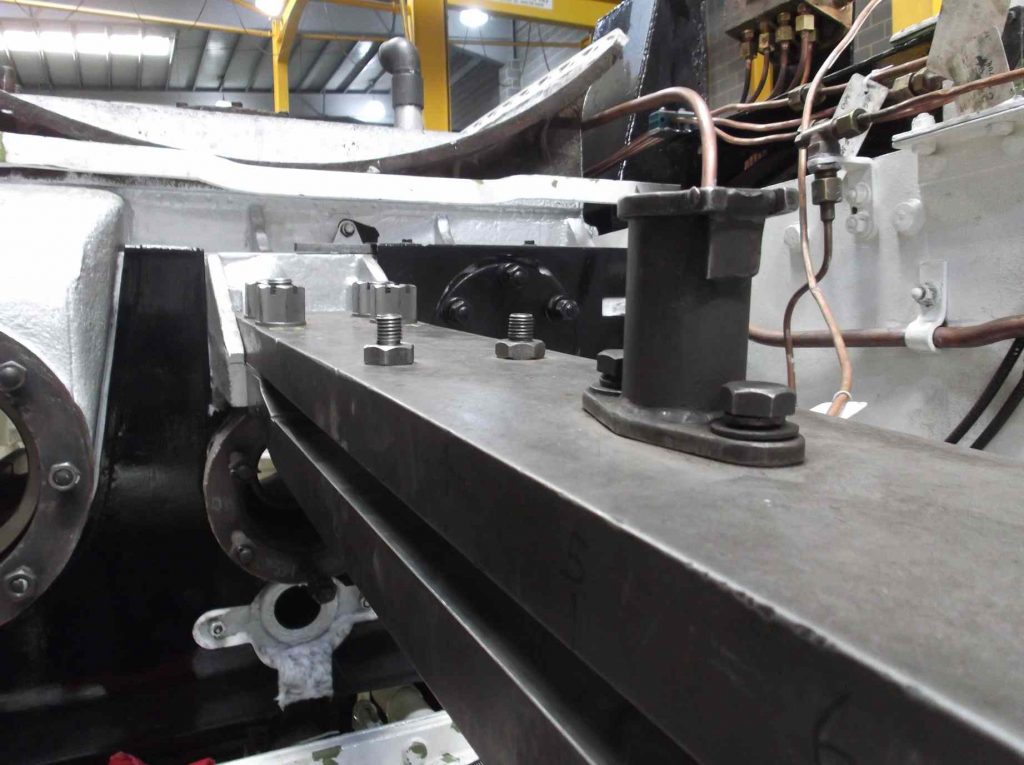
The ashpan was removed so that the new strip added to its front could be welded underneath. The top weld had to be ground flush to match the foundation ring and we were concerned about the strength of the weld. The ashpan came out relatively easily and was put in front of the loco. It has now welded it all along.

Before the fitting of the tender tank, the pipework in the tender frames was pressure tested. When this was completed the piping team moved on to testing the pipework through the loco frames. During testing it was found that one of the few reused sections of pipe had small cracks on one of the bends. This section of pipe ran behind the ashpan, so it was fortuitous that the ashpan had been removed. The section of pipe was replaced with new and the pipe has successfully been tested as pressure tight. Pressure testing of the steam heat pipe run is ongoing. With this close inspection of the pipe runs it has also been identified that some additional clamping will be provided.
At Llangollen the superheater on the boiler has successfully passed its hydraulic test, and that preparations are now being made for the boiler’s final out of frames steam test.
At Cranmore the coach is approaching completion and is now being painted.
Weeks commencing 30 September and 7 October
The big news of this report is the successful out of frames boiler steam test at Llangollen. The problems we had with the manifold and in particular the steam heat valve have now been overcome. The steam heat valve being a new replacement. The safety valves were fitted and adjusted, and operated very well, popping and closing very cleanly.
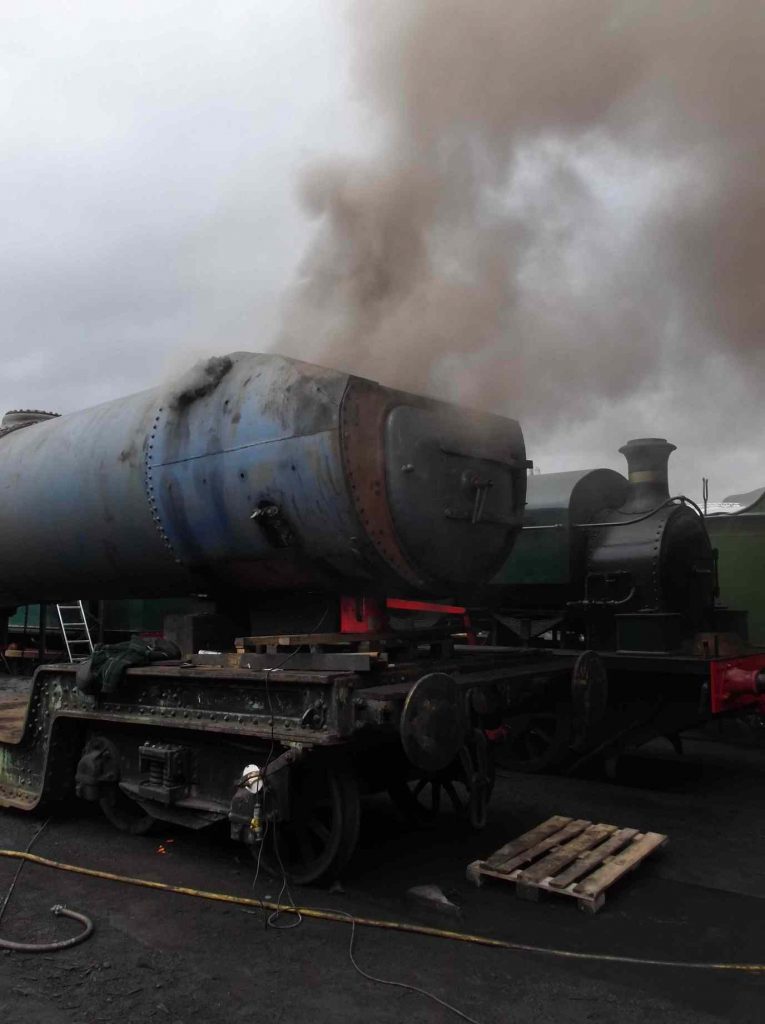
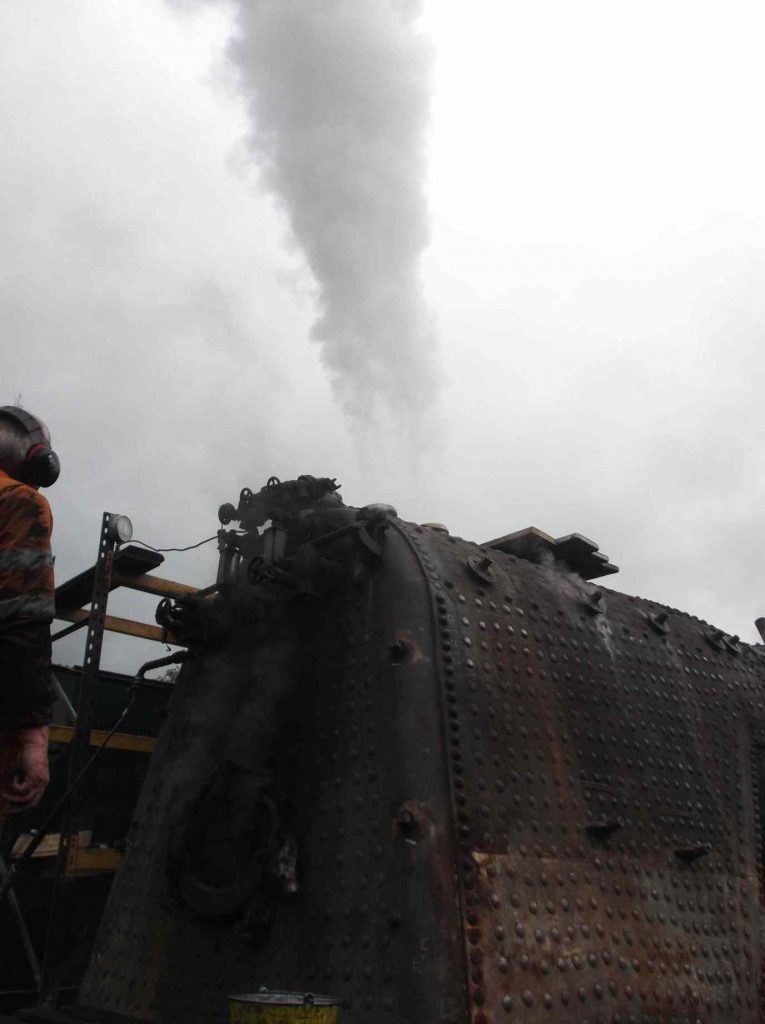
There were still a few fizzes but Llangollen are confident that a period of steaming over the following week will get all that sorted out. Our man in Llangollen had the situation well under control, and the representative from our mainline certification body was pleased with the boiler. Transport of the boiler to York and fitting to the frames is now being planned in detail.
Work has continued on pressure-testing the pipe runs through the loco frames. It’s also been a useful process to revisit some of these pipe runs as we have made a few modifications. One of the pipe unions that runs along the frames near the ashpan was removed and replaced with a soldered connection. We certainly won’t have that joint work loose. Also some additional clipping of the pipes has been put in. One interesting find under pressure test was a malleable iron elbow was found to have a crack in its body. The fitting has been replaced.
The remaining long tender brake pulls were di-penned. No faults were found so they were painted and have now been mounted on the tender. The Painting Team been busy painting all the other tender brake bits stacking up to be fitted. The tender tie rods are now fitted, the tender vacuum cylinder links and the tie bar on the leading intermediate brake hangers. The hornstays are now being painted now they are finally pinned, and the finishing touches being made to the inside of the frames.
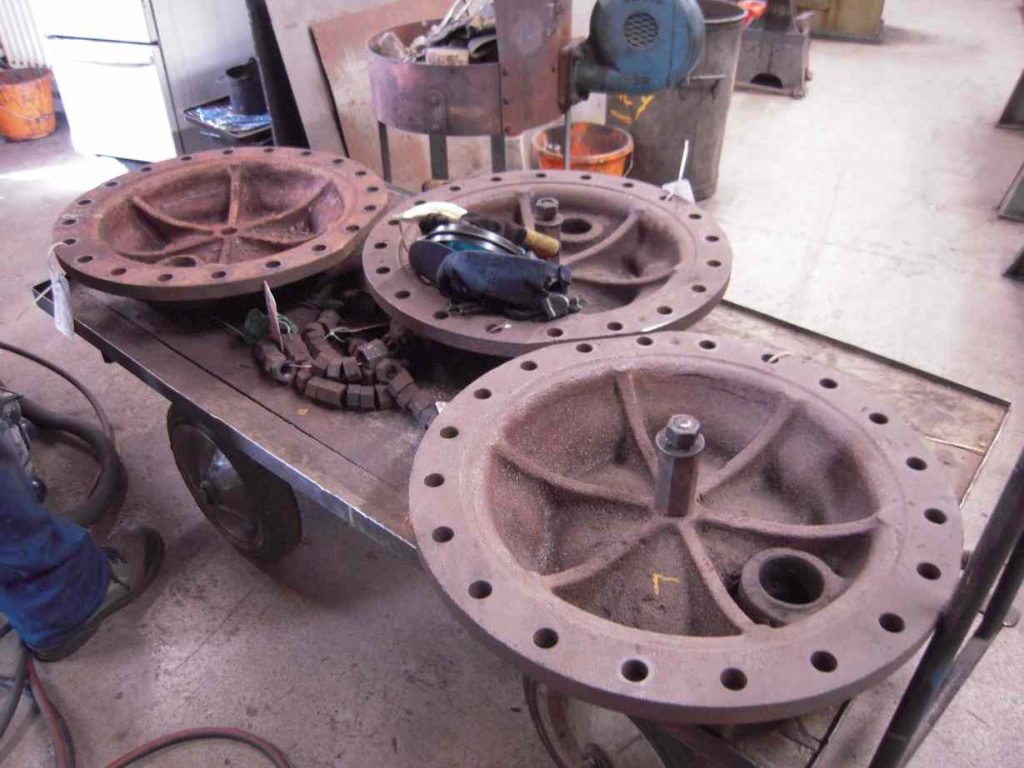
With the hornstays painted the oilier pads can be put in the tender axleboxes. The first 2 pads are now soaking in oil.
The tender adjustable brake pull rods are being painted and will be refitted when they are dry enough. A new pin has been made to replace one that is noticeably worn more than the others. The loco adjustable pull rods have been striped and di-penned. No faults were found but one end of each rod will require re-bushing and all the pins will require replacement. New pins have been made this week and now require cross drilling for split pins.
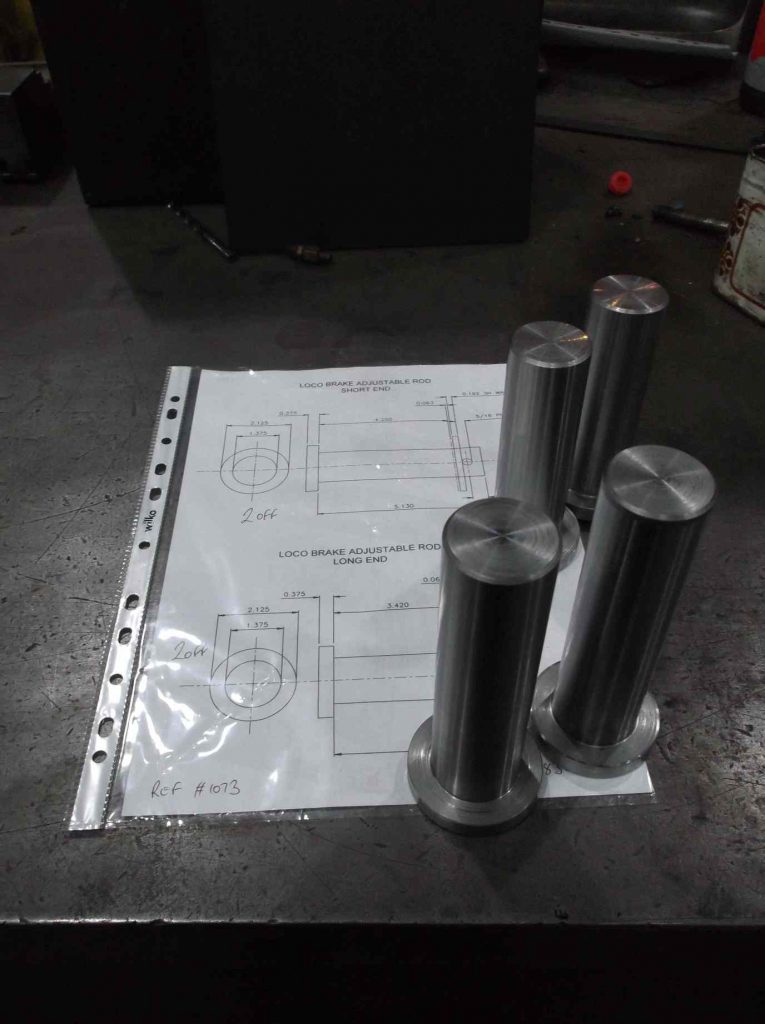
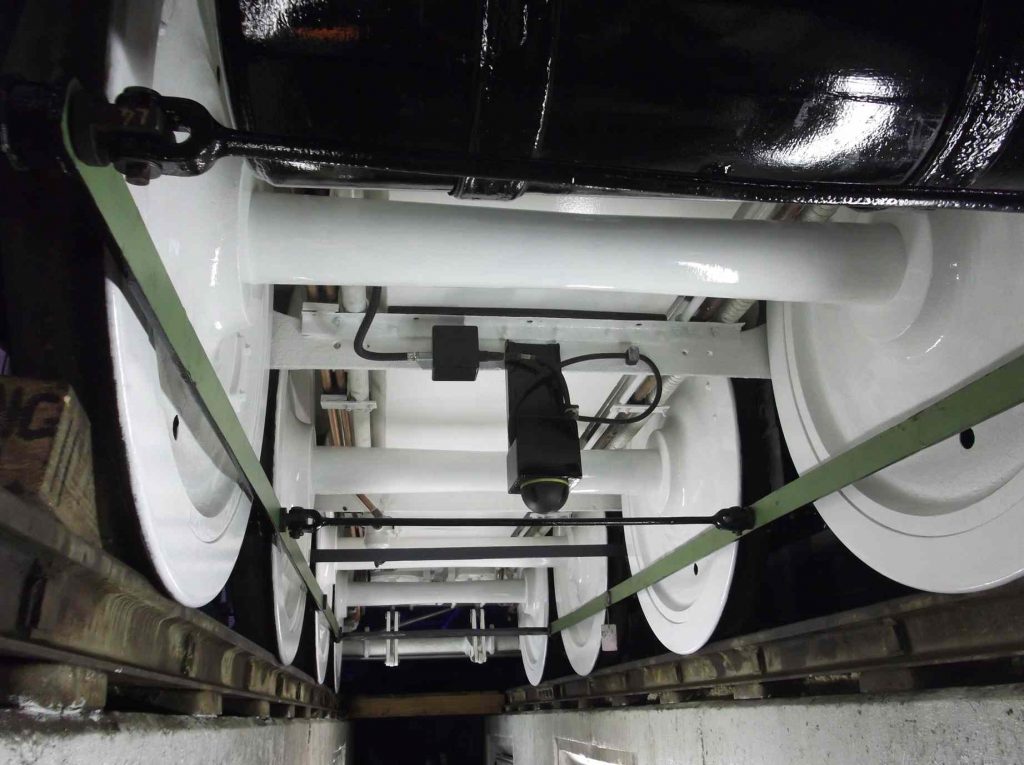
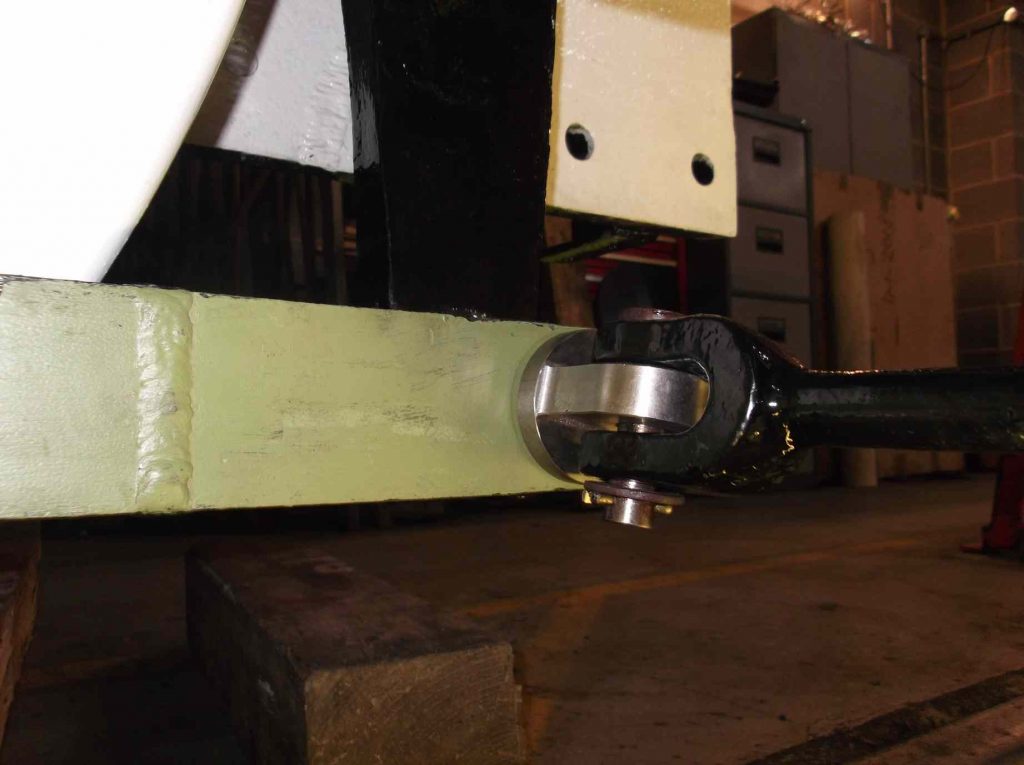
On the inside of the tender frames the TPWS conduit has been re-secured, and the cable re-terminated at the TPWS receiver. Work continues on the OTMR sensor enclosure and the OTMR control unit enclosure and wiring looms.
The tender tank bolts continues with bolting across the front of the dragbox. The front-left corner frame bracket is lower than the dragbox so a shim plate has been fitted. Similarly there is a gap between the rear-left bracket and the tank. In the past these were just wrenched up but we have fitted a shim in here as well. This will reduce the chance of damaging the brackets.
The tank is also bolted to the frames from the inside of the water space. These bolts have to be watertight so Andy Heald has cleaned out all the holes and the surface in the tank where the bolt heads will be sealed. He finished his time in the tank by giving it a good clean out.
Work continues on the tender front steelwork, with new steel now being put in the handbrake shelf. The new plate where the water scoop handle used to be is now replaced. The rear of this space is a corrosion trap so a new plate is being put in to close off any gaps and cavities that can collect wet coal dust. The plates are being drilled and countersunk for bolting in place.
On the top of the tender around the water filler has been coated in a corrosion stabilising fluid prior to being painted.
On the loco the fitting of the taper pins to the lifting arms has been completed. The new motion pins have also been fitted to the expansion links. The left-hand piston cross head has been taken to contractors for the drop link hole, that connects to the union link, to be bored out. Our reamers wouldn’t touch it as it’s very hard. This is now ready for collection.
The right-hand crosshead is being lapped to its gudgeon pin, ready for fitting in the right slide bars.
In the last report the middle slidebars were fitted and the bolts flogged up and the crosshead fitted. Now the right-hand slidebars are in place with the last few bolts being marked for drilling for split pinning.
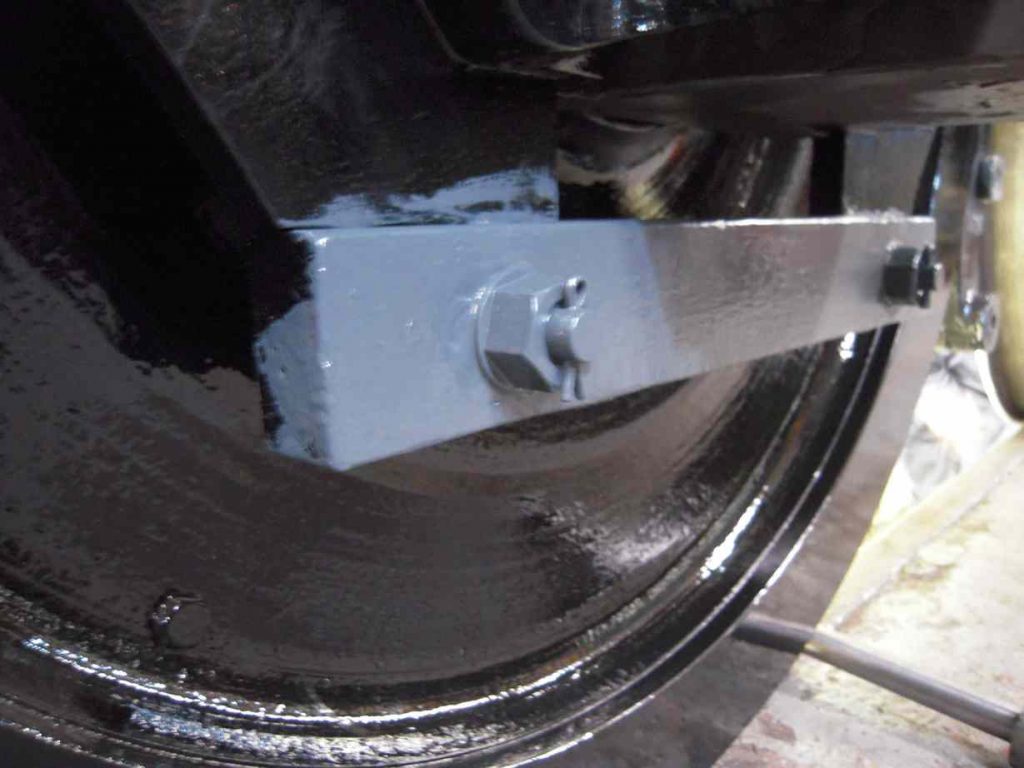
The loco brake hangers continue to be drilled. The old trailing upper pins were removed recently for replacement as they are not recoverable. The holes have been cleaned out on the loco and measured. A drawing was produced and new pins have been made by contractors. They are now being fitted to their locations and the holes through the frames are being reamed.
While the ashpan is out the frames the frames are receiving another coat of gloss. All the pipework in this area has been tested so once the paint is dry the ashpan can now be refitted.
The cod’s mouth gear reassembly continues. The modified and repaired shaft has been fitted and a couple of the bearing housings are being worked on as they show signs of wear from interfering with other parts of the mechanism.
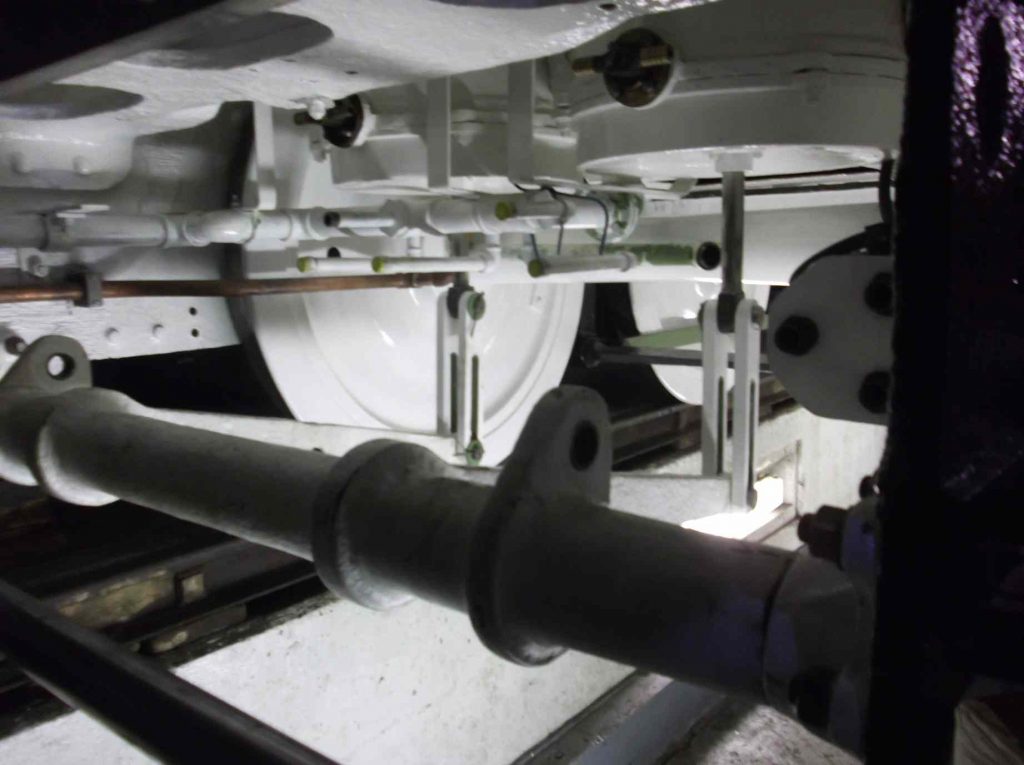
This is the 44th update—you can read all the previous instalments here.