It seems a very odd claim to make—you’ve invented a railway wheel that steers itself, surely that’s what the track is for? But what if the train’s wheels always aligned themselves to the optimum position on the track?
The ActiWheel is a computer-guided wheelset which we’ve borrowed for our future tech exhibition Innovation Platform:
“ActiWheel doesn’t use traditional axles. Instead, every wheel is given its own motor so it can function independently. A computer-based system controls these autonomously, responding to real-time track data to eliminate these issues. No cracks, no noise, no damage.”
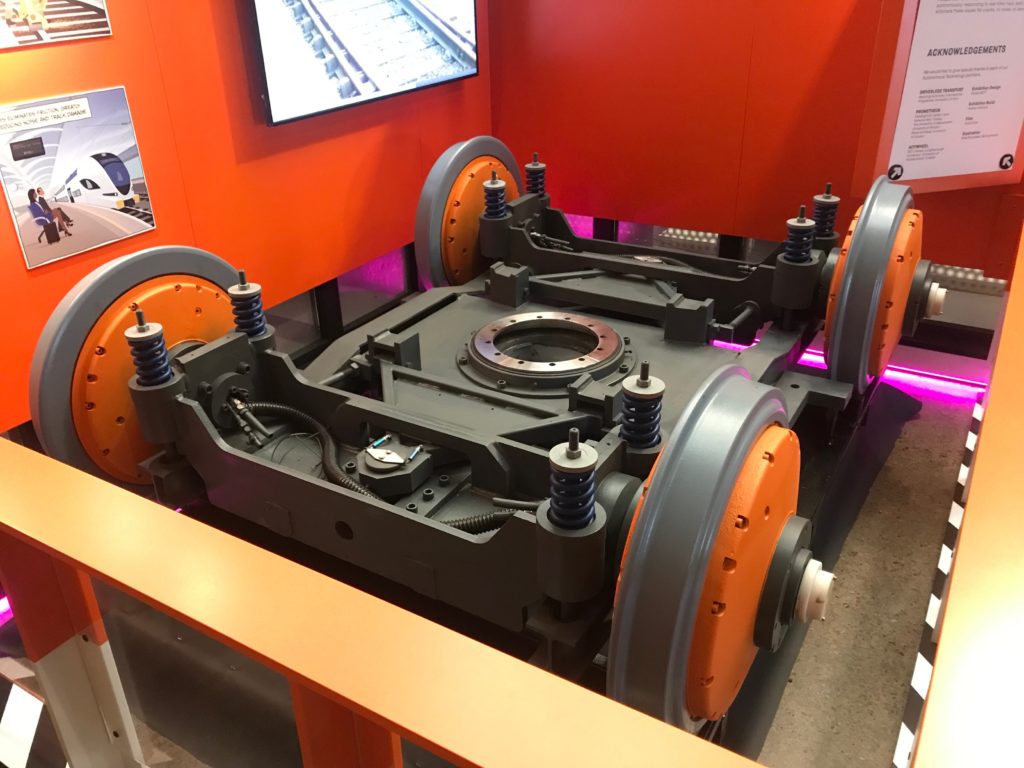
Find out more about Innovation Platform, where you can see the ActiWheel on display until 11 December.
So, why could the ActiWheel be so important?
You would still get all the benefits of a railway (which basically is a way of guiding heavy objects while also reducing the energy needed to move them) and lower the maintenance costs of both train and infrastructure. Also, by controlling the interaction between the wheels and the track you would need less energy to power a train, particularly on curves as there would be less friction. On a curve the rails have to work hard to guide a train as there are centrifugal forces at play pushing the train to one side. Indeed, when a train goes round a sharp curve you often get a horrible screeching sound which is the noise of the flange (the outer edge of the rail wheel above the cone shaped part) grinding against the edge of the rail. With a guided wheel system this should cease. At the same time, you would reduce maintenance costs as the wear on train wheels would become predictable, and there would be less wear on the track.
A guided wheel system should also reduce ‘rolling contact fatigue’ (RCF), which rails may suffer from due to interaction with the wheel. RCF generally appears as small cracks in the rail head and without treatment (by grinding the rail to remove the affected part of it) rails can break. On curves, RCF is called ‘gauge corner cracking’ a phenomenon that track engineers are acutely aware of and not least because of a terrible accident that happened on the East Coast Main Line over 20 years ago.
The Hatfield crash in October 2000 killed four people and injured more than 70. It was caused by rolling contact fatigue/gauge corner cracking because the rails concerned had not been properly maintained. The official investigation led to massive fines for those involved in looking after the railway infrastructure. In the immediate aftermath of the Hatfield crash, 1,800 speed restrictions were introduced, some of which lasted for over a year. In the days following the crash some train journeys took a similar amount of time to when the railway had first opened in the reign of Queen Victoria.
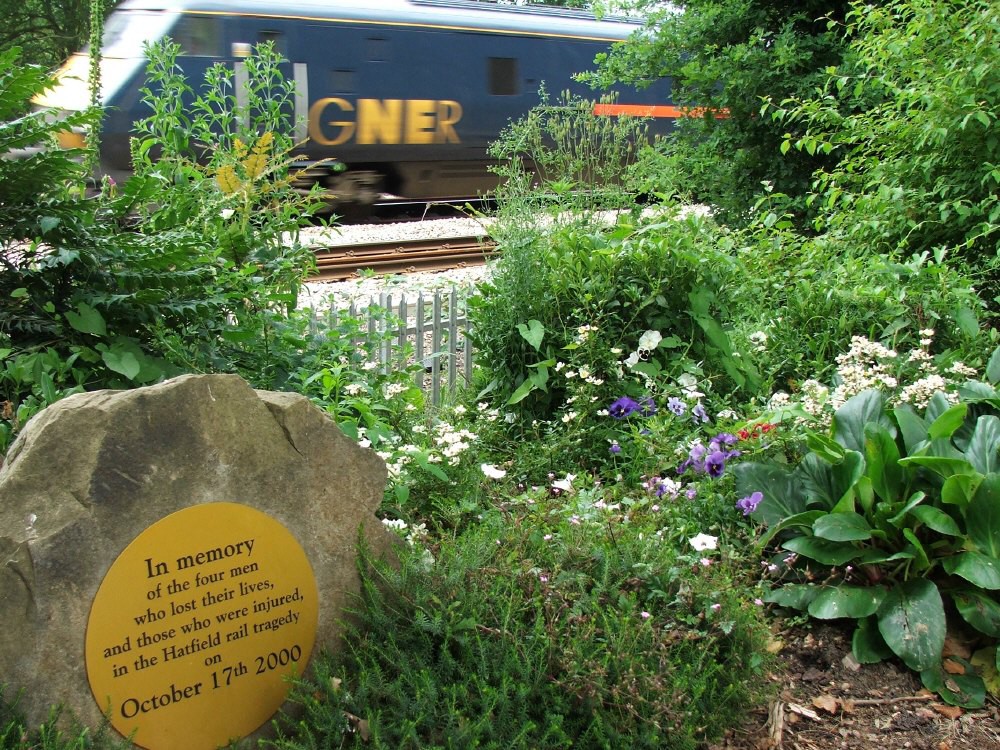
Michael Pead, 2005. Licensed under CC BY-SA 2.0 UK
Ultimately Railtrack PLC was put into administration and Network Rail created—a government owned not-for-profit company to look after Britain’s railway tracks. The late Sir Alastair Morton who was at one time head of the Strategic Rail Authority said Hatfield caused ‘a collective nervous breakdown’ on Britain’s railways.
Following the accident, the Health and Safety Executive collected over 200 pieces of rail from the site to better understand what had caused the crash, in particular the factors relating to material science. Four of these pieces of rail ended up in the HSE Science Division store which holds objects involved in fatal accidents for 20 years, after which they are disposed of. The COVID-19 pandemic delayed the process of disposal which meant that when the HSE were contacted to see if by any chance they had any rail fragments that showed rolling contact fatigue/gauge corner cracking, they were able to let the NRM collect the four rail fragments from Hatfield.
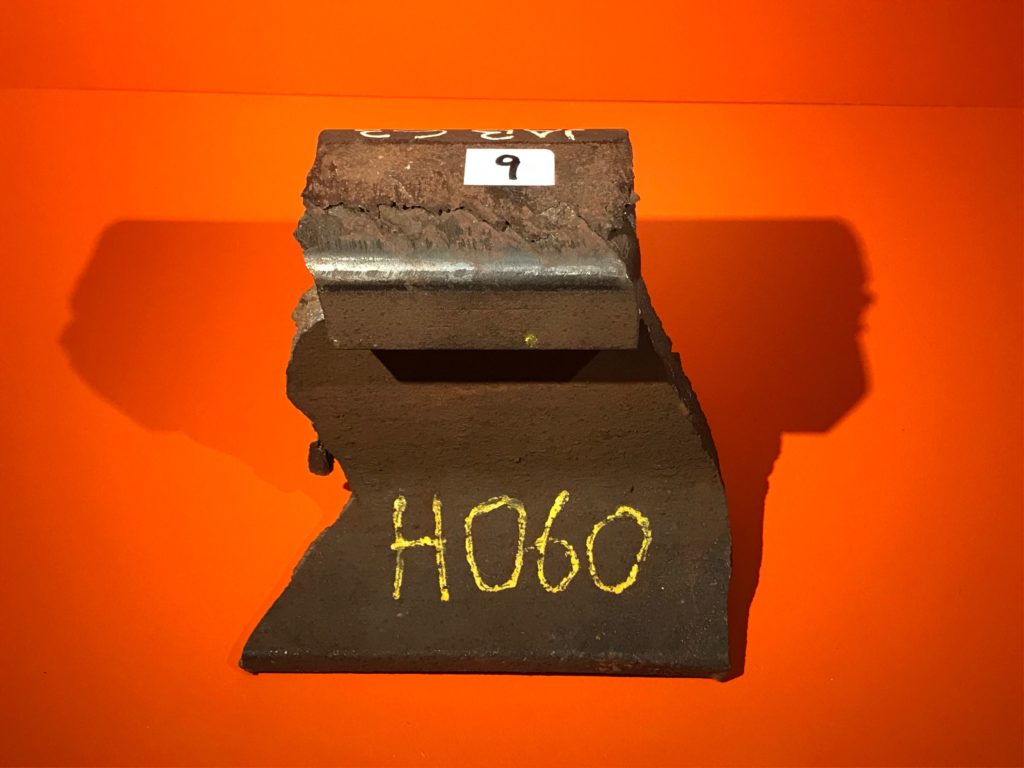
Science Museum Group. Object no. E2022.104.x.
These rail samples show what can go catastrophically wrong between a wheel and a rail, and why a new self-guided rail wheel might have an important role to play in the future of Britain’s railways.
Surely a passive independent wheel, on its own bearing and not tied in a pair by an axle, would give many of the same benefits with less cost and complexity. Much as a differential in a car reduces tyre scrubbing on corners.
I’ve had the same thoughts modeling on O Gauge track. To avoid the outer wheel climbing over the rail on tight bends I needed to check rails, but when I did as you suggest the check rail wasn’t necessary. The only puzzles is why it’s not already common practice.